Ewellix provides effective solutions to complete vertical and horizontal adjustment in a smart way with a wide range of “ready to mount” additional linear axis solutions. We designed them for different applications, giving your robot an extended operational range.
7th axis for robots product range
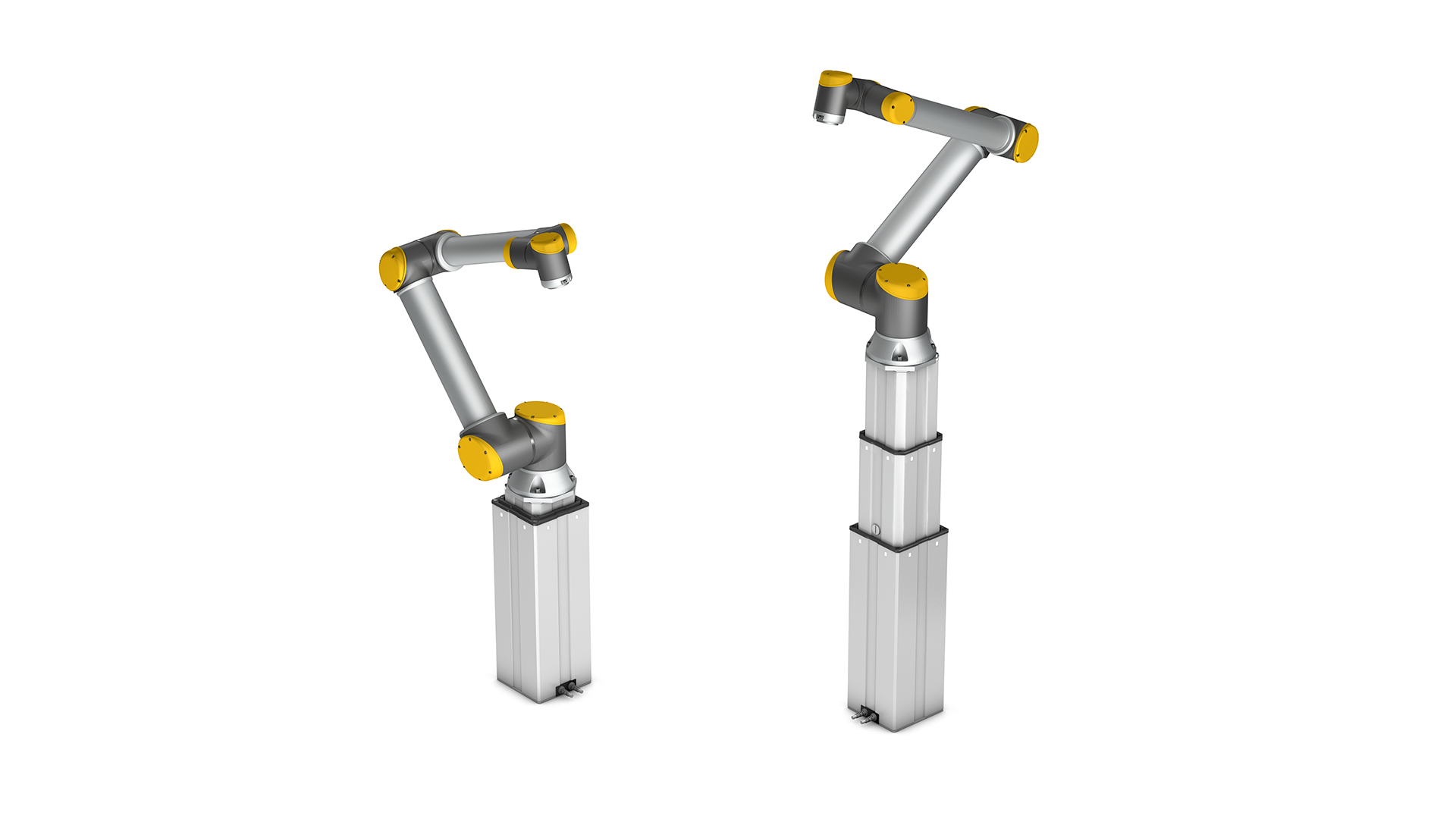
LIFTKIT
- Load up to 1,5 kN and speed up to 80 mm/s
- Stroke up to 1 400 mm
- Plug and play with Universal Robots, Omron, Techman, FANUC, Yaskawa collaborative robots and several palletising software
- Compatible with any robot brand via TCP/IP communication protocol with a plug-and-play script commands
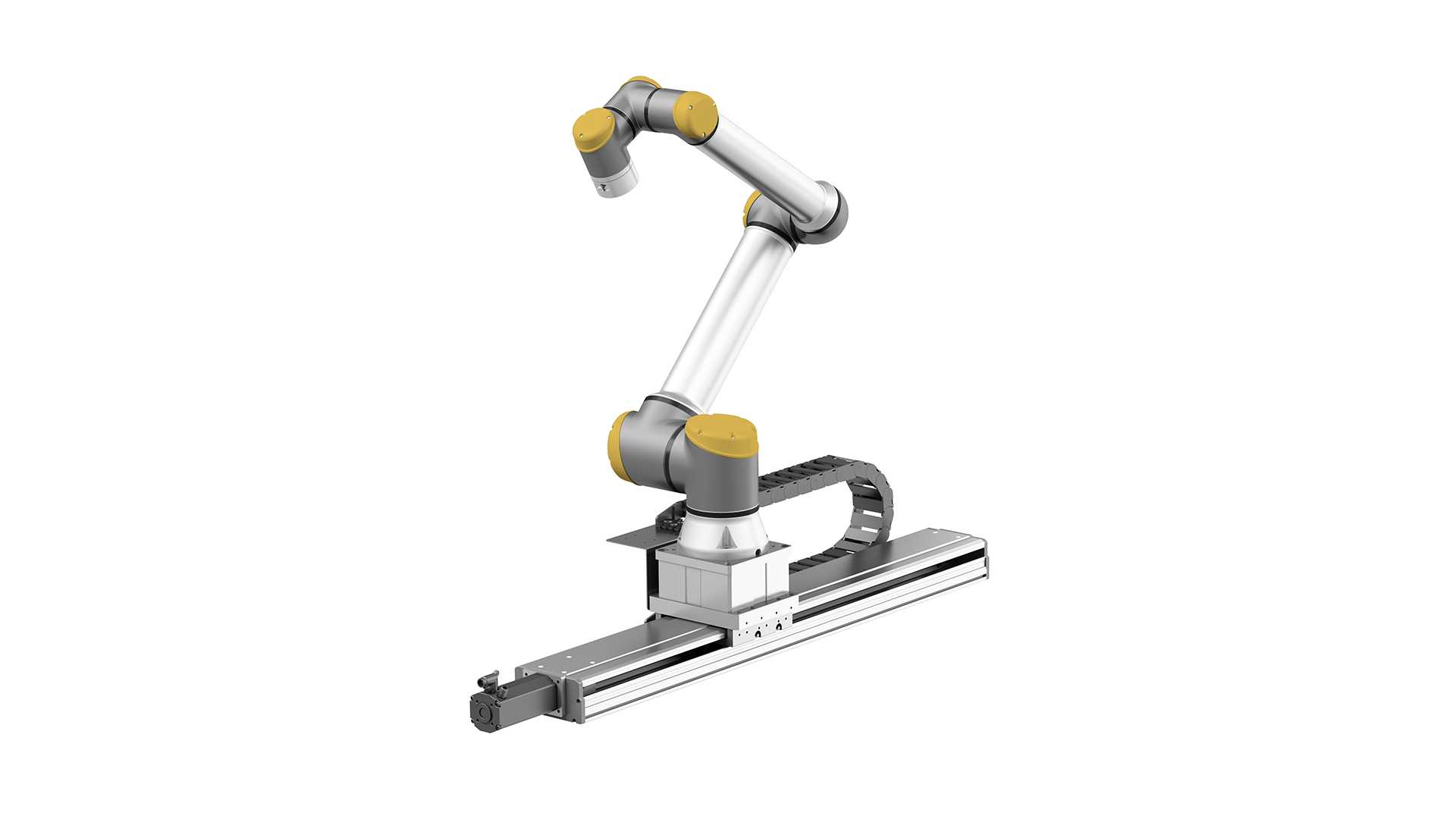
SLIDEKIT 2.0
- Load up to 10,9 kN and speed up to 1 000 mm/s
- Stroke up to 3 000 mm
- Plug and play with Universal Robots
- Compatible with any other robot brands via I/O commands up to 14 x configurable move-profiles
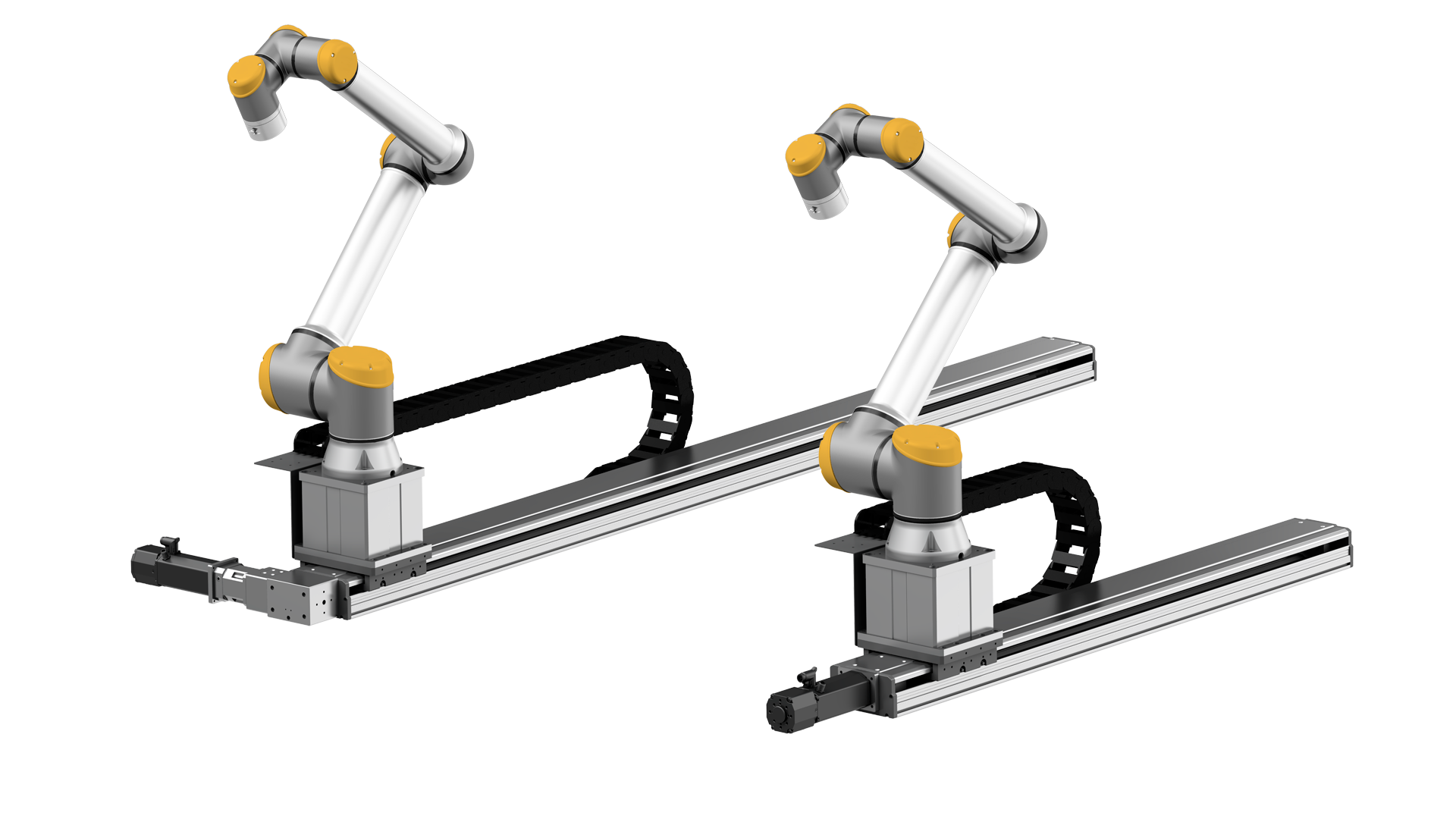
SLIDEKIT 2.0 0S
- Load up to 16 kN and speed up to 1 000 mm/s
- Stroke up to 3 000 mm
- Ethernet TCP/IP communication protocol
- Compatible to large size cobot up to 75 kg
Video
Motion talks - Boost your capabilities with 7th axis solutions
Smart 7th axis solutions for collaborative and industrial robots
Read more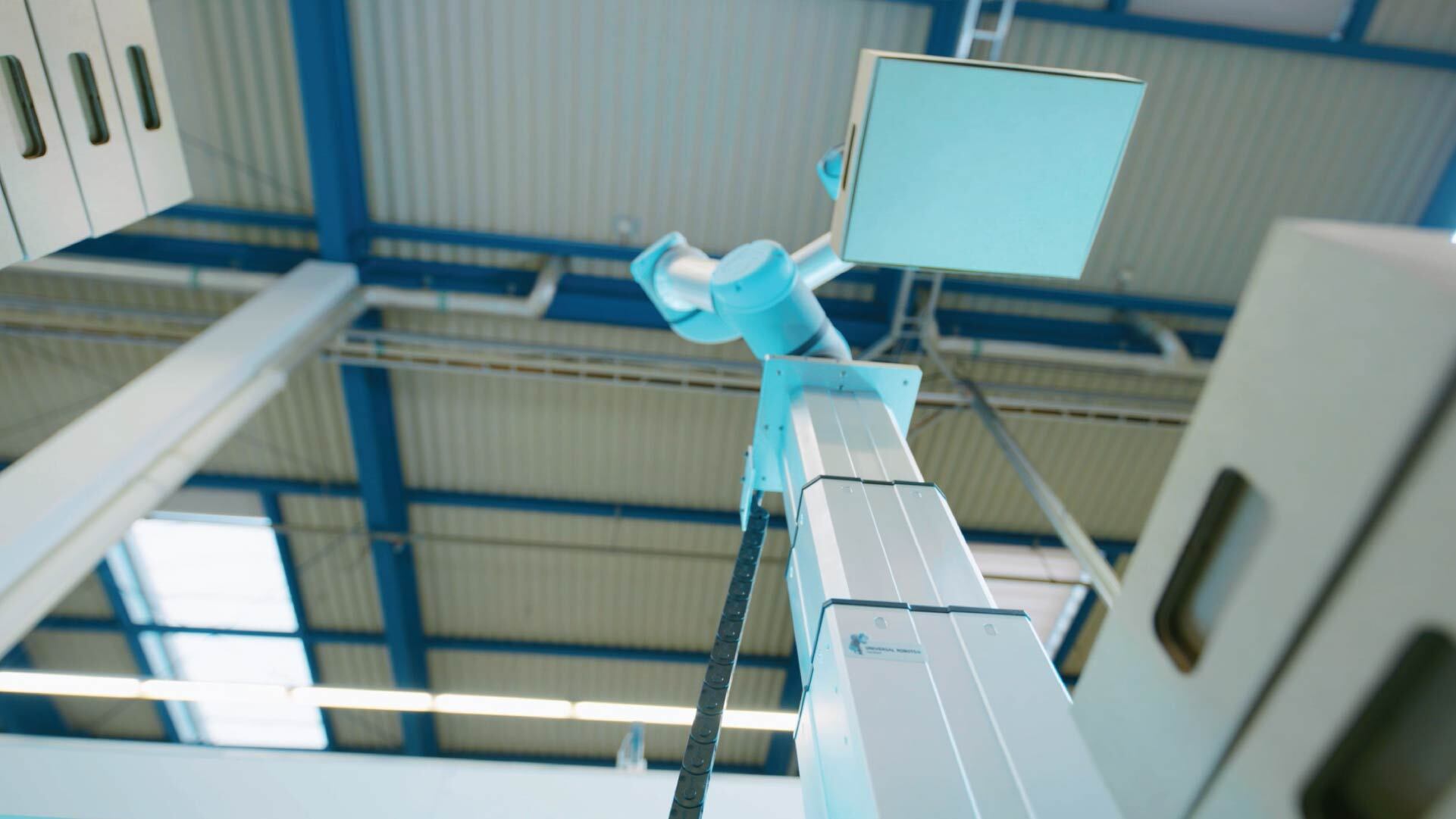
Frequently asked questions
While the vertical axes LIFTKIT may be primarily used for end-of-line palletizing and depalletizing – along with other applications such as controlling, scanning, and painting - the SLIDEKIT offers a wider range of applications, including welding, polishing, and machine tending, making it a more versatile option overall. Additionally, the SLIDEKIT's ability to manage multiple pallets with one robot adds additional value and efficiency. For example, a manufacturing facility may use the Ewellix LIFKIT on their robotic arm to perform welding on multiple parts simultaneously, and the robot's limited range will no longer be an issue with the SLIDEKIT covering all welding zones and configurations. In another example, in a logistics warehouse, the LIFTKIT could be used with a robot to efficiently move and stack pallets of different sizes up to 2.8 m high, improving warehouse organization and optimizing space utilization.
The LIFTKIT and SLIDEKIT are types of 7th axis robots that have been specifically designed to work with collaborative robots, specifically robot arms. The LIFTKIT, with its vertical axis, is capable of handling cobot variants weighing up to 160 kg and reaching maximum speeds of 1 m/s (robot's speed). The LIFTKIT maximum speed for vertical movement is 80 mm/s, with a stroke range of 1400 mm. On the other hand, the SLIDEKIT, with its horizontal axis, can handle cobots weighing up to 75 kg without payload and up to 90 kg with payload. It has a maximum stroke of 3 m, with the option for a higher stroke upon request, and the SLIDEKIT's maximum speed of 1 m/s.
The SLIDEKIT and LIFTKIT range extenders are designed to seamlessly integrate with existing robot lines, allowing for easy installation and operation. Our plug-and-play solution eliminates the need for extensive engineering work, saving our clients time and resources. The graphical user interface and script commands library make it simple for users to control the range extender directly from the robot environment, enhancing efficiency and productivity in their operations. We also provide SLIDEKIT as well as LIFTKIT in the generic version we refer to as 0S. The customer can easily control this range extender version via Ethernet TCP/IP communication protocol via socket messaging by using a rich script commends library. For example, a robotics company looking to extend the range of their robot arm could simply purchase the SLIDEKIT or LIFTKIT range extender, plug it in, and use the provided graphical user interface to operate it without needing to dedicate hours to engineering a custom solution. Additionally, if they prefer more control, they could opt for the generic 0S version and easily communicate with it via Ethernet TCP/IP using the provided script commands library.
We make our offer as easy to integrate as possible, which is why our LIFTKIT and SLIDEKIT hardware includes safety inputs connected inside our control box, enabling a safety stop. All of the robot's stop orders—soft stop and emergency stop—interact perfectly with the plugin software. When the application starts up again, the range extender pauses and starts moving again from the point where it stopped. Ewellix provides a component for the application for the risk analysis to be done by the system integrator or OEM to ensure that the whole installation meets the local safety requirements. We can provide support on our components during the implementation.
Need more
information?
Ask our experts.
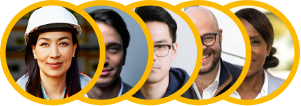